Implementing Lean Solutions
Our Approach
Whether in a strategic level in a boardroom or with sleeves rolled up on a shop-floor or back office, AHGms has a proven track record delivering waste reduction and cost improvement projects across multiple sectors.
At AHG Consultancy, we bring nearly 30 years of experience in implementing award-winning Lean systems and delivering top-notch Lean Training to businesses and individuals. Our expertise spans across various sectors, from Manufacturing to the Public Sector, from Corporate Back offices to SMEs, and from Global Multinationals to startups.
Our team comprises seasoned professionals with a deep understanding of Lean principles and a strong commitment to driving operational excellence. We have a proven track record in Lean Operations and Lean Training, and we are dedicated to helping you optimise your business processes and enhance your team's capabilities. We recognise that every organisation is unique, and we customise our solutions to meet your specific needs.
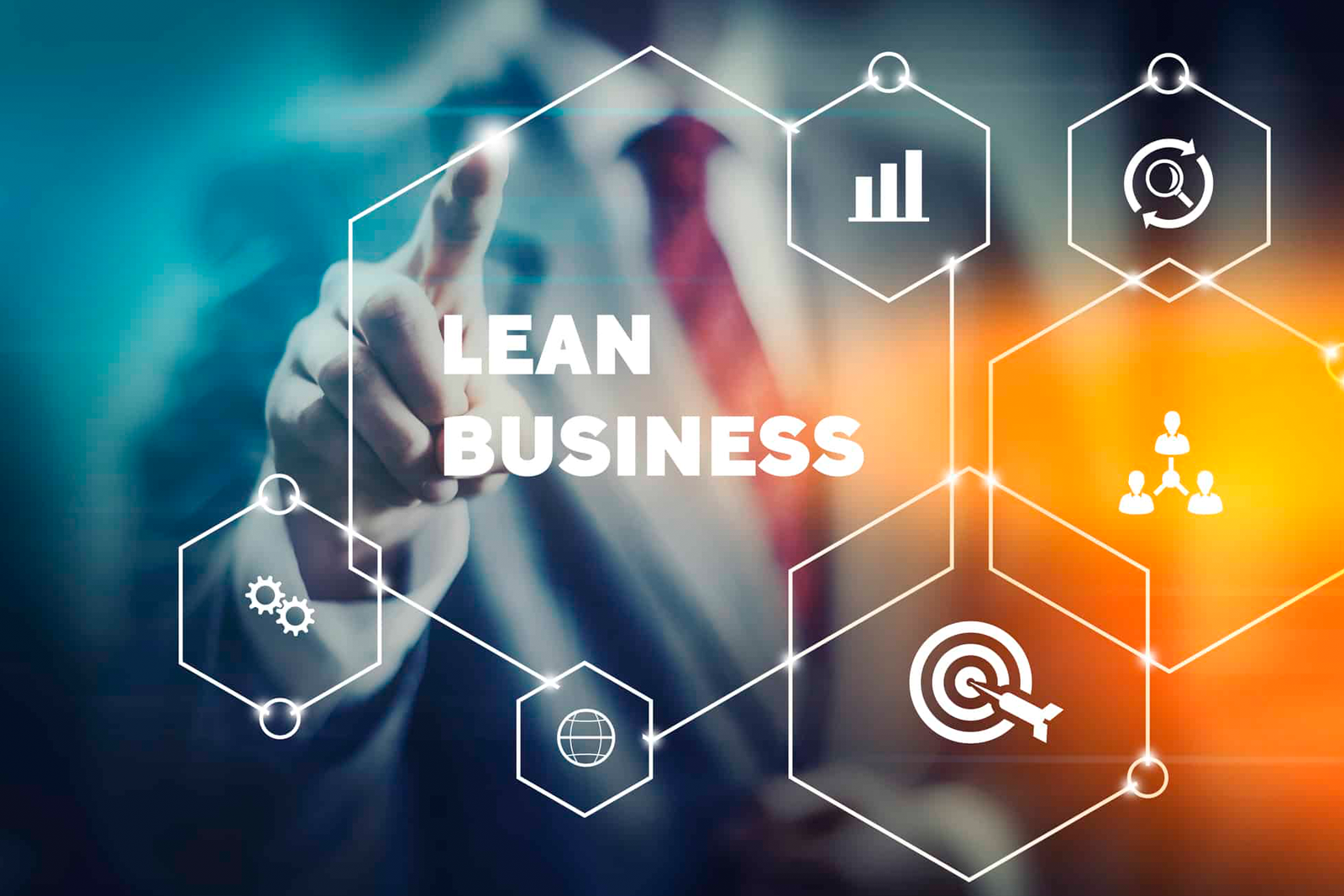
Lean Operations & Lean Training
Lean Operations
At AHG, we leverage a variety of Lean tools and techniques to revolutionise your business operations. The following have been successfully implemented in numerous organisations across diverse sectors
· Value Stream Mapping (VSM): A visual representation of your processes that helps identify and eliminate waste, improving the flow of value to customers.
· 5S Methodology: Sort, Set in order, Shine, Standardise, and Sustain. This technique enhances workplace organisation, cleanliness, and efficiency.
· Kaizen Events: Short-term, focused improvement projects that bring together cross-functional teams to address specific problems.
· Kanban: A visual system for managing work as it flows through your processes, ensuring work is pulled only when there is demand.
· Poka-Yoke: Error-proofing techniques to prevent mistakes in the production process.
· 5 Whys: A problem-solving technique that delves into the root cause of an issue by asking "why" repeatedly.
· Standardized Work: Establishing a consistent and repeatable way of performing tasks to enhance quality and efficiency.
· Takt Time: The rate at which products need to be produced to match customer demand.
· Hoshin Kanri: A strategic planning and management process that aligns an organisation’s goals and objectives.
· Jidoka: The ability to detect and rectify abnormalities in the production process, preventing defects from occurring.
· Muda: The identification and elimination of non-value-added activities or waste.
· Total Productive Maintenance (TPM): A comprehensive approach to maximise the efficiency and effectiveness of equipment and machinery.
· Visual Factory/Workplace: Utilising visual cues and indicators to enhance communication and workflow.
· SMART Goals: Specific, Measurable, Achievable, Relevant, and Time-bound goals to guide improvement efforts.
· Just-In-Time (JIT): The concept of producing and delivering the right quantity of products at the right time to meet customer demand.
Lean Training
Our comprehensive Lean Training programs encompass key tools and techniques, such as:
· PDCA Cycle (Plan-Do-Check-Act): A continuous improvement methodology used to identify, implement, and control changes in processes.
· Root Cause Analysis: A structured approach to identify the underlying causes of problems and prevent their recurrence.
· Value-Added vs. Non-Value Added Analysis: Distinguishing activities that add value to the customer from those that don't.
· Gemba Walks: Observations on the shop floor to understand current conditions and identify improvement opportunities.
· A3 Problem-Solving: A structured problem-solving approach that fits on a single A3-sized sheet of paper.
At AHG, we leverage a variety of Lean tools and techniques to revolutionise your business operations. The following have been successfully implemented in numerous organisations across diverse sectors
· Value Stream Mapping (VSM): A visual representation of your processes that helps identify and eliminate waste, improving the flow of value to customers.
· 5S Methodology: Sort, Set in order, Shine, Standardise, and Sustain. This technique enhances workplace organisation, cleanliness, and efficiency.
· Kaizen Events: Short-term, focused improvement projects that bring together cross-functional teams to address specific problems.
· Kanban: A visual system for managing work as it flows through your processes, ensuring work is pulled only when there is demand.
· Poka-Yoke: Error-proofing techniques to prevent mistakes in the production process.
· 5 Whys: A problem-solving technique that delves into the root cause of an issue by asking "why" repeatedly.
· Standardized Work: Establishing a consistent and repeatable way of performing tasks to enhance quality and efficiency.
· Takt Time: The rate at which products need to be produced to match customer demand.
· Hoshin Kanri: A strategic planning and management process that aligns an organisation’s goals and objectives.
· Jidoka: The ability to detect and rectify abnormalities in the production process, preventing defects from occurring.
· Muda: The identification and elimination of non-value-added activities or waste.
· Total Productive Maintenance (TPM): A comprehensive approach to maximise the efficiency and effectiveness of equipment and machinery.
· Visual Factory/Workplace: Utilising visual cues and indicators to enhance communication and workflow.
· SMART Goals: Specific, Measurable, Achievable, Relevant, and Time-bound goals to guide improvement efforts.
· Just-In-Time (JIT): The concept of producing and delivering the right quantity of products at the right time to meet customer demand.
Lean Training
Our comprehensive Lean Training programs encompass key tools and techniques, such as:
· PDCA Cycle (Plan-Do-Check-Act): A continuous improvement methodology used to identify, implement, and control changes in processes.
· Root Cause Analysis: A structured approach to identify the underlying causes of problems and prevent their recurrence.
· Value-Added vs. Non-Value Added Analysis: Distinguishing activities that add value to the customer from those that don't.
· Gemba Walks: Observations on the shop floor to understand current conditions and identify improvement opportunities.
· A3 Problem-Solving: A structured problem-solving approach that fits on a single A3-sized sheet of paper.